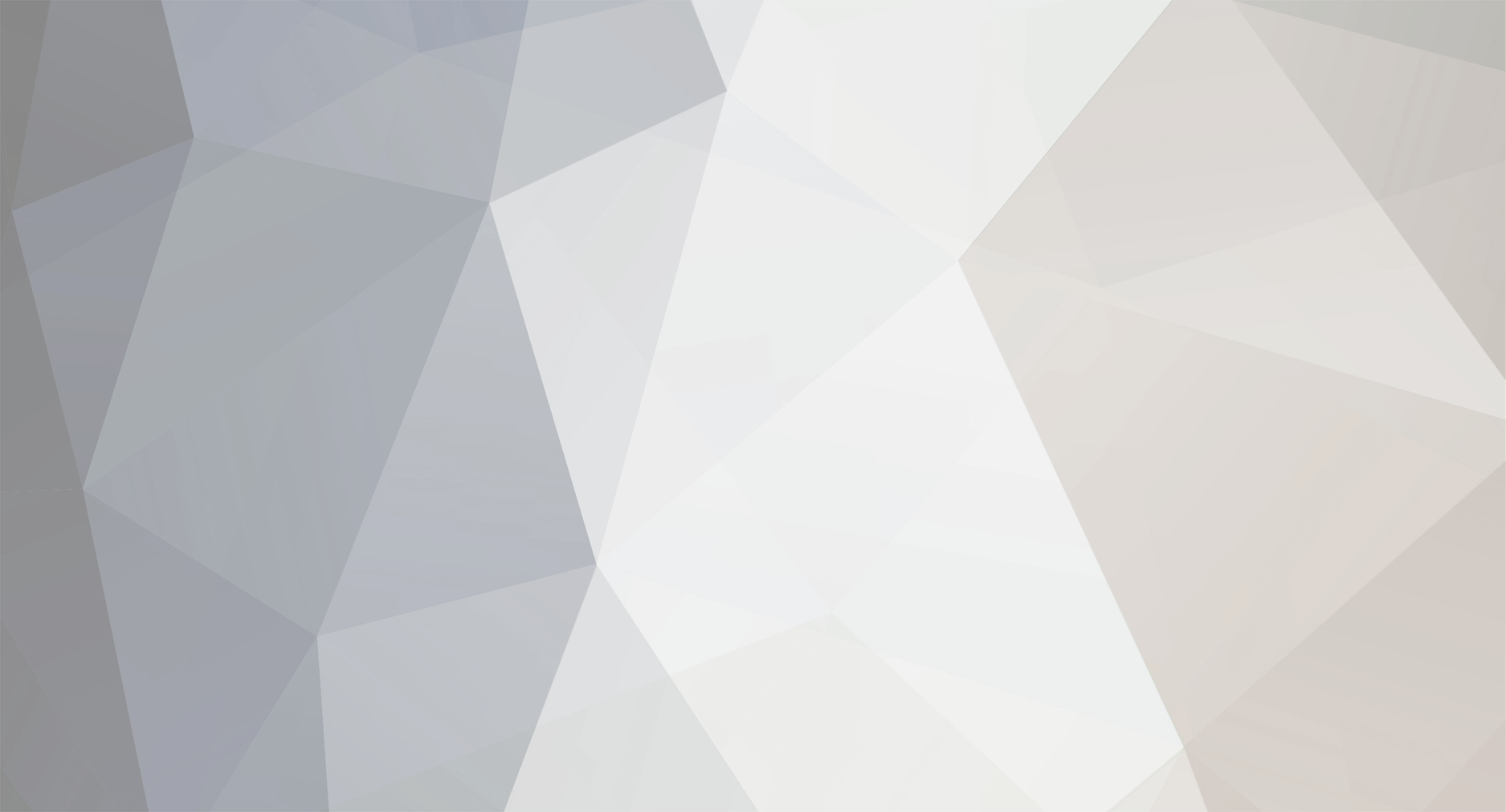
TuffguyF4i
Members-
Posts
10,359 -
Joined
-
Last visited
-
Days Won
57
Content Type
Profiles
Forums
Gallery
Events
Everything posted by TuffguyF4i
-
How to: Build your own custom LED Tail Lights
TuffguyF4i replied to TuffguyF4i's topic in The Garage
Good catch,,,you're right. Will update! -
How to: Build your own custom LED Tail Lights
TuffguyF4i replied to TuffguyF4i's topic in The Garage
Now you have all of the hot wires soldered and all of the ground wires soldered. Test each circuit with a 9V battery. Reversing the poliarity will not hurt the LEDs. You can't blow anything up. Now what you are going to do is solder all of the like wires to each other and make them have one common wire. What you want is 1 ground wire and 1 brake light wire (hot). I joined all of the ground wires together and soldered them to a large black wire. I joined all stripped wires together and attached another stripped wire. Feel free to shrink wrap or electrical tape wrap the ground wires connection. You're done with it. So where the hell does my other wire come from? Right now i have just a ground wire and a brake light wire. I need running lights. Well here's the scoop...but first you need to learn about diodes. Diodes: Diodes allow voltage to flow one way and not another. By installing diodes, you will be able to prevent any fuses blowing when you apply the brakes or have your running lights on. You will be installing another wire with resistors and diodes at the same connection where all of your hot, brake light wires come together. Every diode has a line on it. You want to point that diode toward the circuit you need to energize. Think of that diode as blocking the path, back to the bike but letting it go to the lights. I used two soldered in parallel to make sure I have enough current protection. Put that aside for a second and solder your resistors. Again, these are two 100ohm 1/2W resistors which make up 50ohm is total resistance. In parrallel they provide 1 W protection. Now solder the resistors and diodes together. It doesn't matter which goes first. Solder the diodes and resistor to the bundle of hot wires that come from the brake circuits. Remember: the line on the diodes must face the circuit on the board. Wrap the connections in shrink or tape. This is what my wires now look like. Black = Cluster of ground wires Red = Running light (diodes and loose 100ohm resistors, hooked to the stripped wires) Stripped wire = Brake light (circuit on the board with 46 ohm resistors) If you have a battery nearby (12V car or bike), go ahead and test to make sure it all lights up. Success!!! If you did things right, you should be nearly blinded by looking directly at the brake light. Its pretty insane! Now you need to hook up the completed LED board to the bike. I chose to solder my wires to the connector. Here is what your connector looks like. Here is what wires go where. Make sure you get enough heat into the connector so the wires bond well. Tug on them so you can make sure everything is sound. Now you need to secure the board to the housing. I used a hot melt glue gun. It came out looking pretty clean!! Place the lens back on the housing and head to the garage to make sure it works before you glue the lens to the housing. running light brake light RTV the lens back onto the housing and you should be good to go. Enjoy your added visiblity on the street!!! -
This guide is intended to be simple and straightforward. It's intent is to show you how to build a simple dual intensity brake light LED board. I have completed 6 assemblies using the same components that I am listing for this build, with great success and not one LED failure. Feel free to ask questions if you need something clarified... i'll re-edit the post and make things more clear. Tools/supplies needed: -good soldering iron -solder with resin core (helps solder adhere and clean) -good small wire cutters -wire stripper -small gauge wire (18-20) -chrome spray paint -Radio shack diodes (1/2W each) -Radio shack resistors (46 Ohm 1/2Watt and 100 Ohm 1/2Watt) -Radio shack perf board (more on this later) -Superflux LEDs (about 30-60 red/orange superflux. Use genuine Lumileds. www.LEDCAR.com Part number: HPWT-DH00-G4000) You can also find people selling them for $15-20/per 60 on HID planet. -Holiday red, green and blue table cloth. Merry Christmas. Resistors: Basically, the more resistance the less light. So I chose 46 ohm 1/2Watt resistors and 100 ohm 1/2W resistors. I chose to run 4 LEDs in each circuit. I will hook the resistor up to the + side of the circuit and then wire each LED in series. At the end you see a purple ground wire (eventually hooking up to a big black ground wire). Here is the circuit. You can see from the schematic, that there are two circuits. One for brake and one that is always on for the running light. The brake light bypasses the 2x100ohm resistors (50ohm) and uses just the 46ohm resistor. (less resistance = more light) For the running light you have the 2x100ohm resistor and the 46ohm resistor. This gives you a total resistance of 96 ohms for the running light. When resistors are in series, you can simply add the resistance. What thought process went into this? I first calculated what would be safe current and voltage to run through the circuit of 4 LEDs. Then i figured out what looked good. It is safe to run as low as 36 Ohm for the brake light. This will make it just slightly brighter, but will run more current through the LED, and could decrease life. The combination of the 100ohm and 46 ohm to give me 96ohm total resistance for the running light was not calculated. I tried to see what would make the light significantly dimmer. This worked. So,,,on to the build..... Typical housing. I actually have a 50LED strobe that replaces my lower bulb. Ignore. It does not affect this build. Heat the oven to the lowest temperature it will go. For my oven that is 250 Degrees F. DO NOT PLACE THE ASSEMBLY IN THE OVEN WHILE IT IS HEATING. The oven gets significantly hotter in certain spots. Preheat. Place the assembly in after the oven is heated. Leave in there for 10 mins. Pry the lens from the housing. For me, this retrofit will be for the top bulb only. Grab your Radio Shack perf board (common item) and hold it up to where it needs to fit. Trim the perf board to fit. I used a big dull set of wire clippers. The Dremel makes a huge mess. Smooth the edges with the Dremel. Make sure you take a good long look at the angle this board will need to sit. If you direct the board straight forward, it will be very upright when mounted on the bike. I'd recommend doing the trimming of the board with the housing on the bike. When you are happy with the size of the board, give it a light coat of chrome spray paint. Only paint the side that the LEDs will be mounted on. Traffic facing side. Now we're getting somewhere... I hit the paint with the heat gun so that the paint bakes on and dries quickly. But if you can wait an 2 hrs, thats cool too. Place your LEDS in a pattern that you like. Think ahead, since you will need to link them together in pairs of 4. Make sure you have a number that can be divided by 4. 8, 12, 16, 20, 24, 28....you get the idea. You can put as may circuits on this board as will fit your budget. That is up to you. I believe I chose 24 or 6 circuits of 4. Now,,,while you are placing them, keep in mind they should all be placed facing the right direction. Why? Time for some LED 101. Here is how they come,,,in a tube of 60. Notice they have 4 contacts. 2 postive and 2 negative. You only need to hook up 2 contacts. 1 positive and 1 negative. Four contacts are there for heat dissipation and for ease of hooking the LED into a PCB. Don't worry, it will be fine with 2. Important: The positive side of the LED is the side with the two small holes through the metal on the inside of the lens. You can see this in the pictures. Here is how you will end up wiring them up. (more on this later) Not sure why i picked this pattern,,,but it ended up looking good. The LED's are now all loosely stacked into the board in the pattern you like. Place a hardcover book on top of them, and flip the board over, so they will not all fall out. Now bend over the ends of the LED leads, so they stay on the board. Your circuits should look like this, repeated as many times as you need. When you are done, it should look like this. The wires sticking up are the resistors. I wired them through the board to make things neat. You will solder a wire to each of these resistors. This will be ultimately attched to the brake light. This is your 46 ohm circuit. Ground wires soldered to the end of each circuit (purple wire) Brake light wire soldered to each resistor (striped)
-
I have plans to do my XX this winter. Do you guys think i could get ahold of this kit? I will probally do my cousins F4i at the same time. Would it take the same size of shims? Either way, i'll contribute whatever the acceptable amount is to the bank. Where do you order shims from?
-
I should have clarified initially,,,thank you. The pedal goes down farther than it should. With the car running (power assist) i can't build pressure. The pedal yields resistance but not what it used to. That is what led me to believe i had some sort of internal master cyl. leak. My wife was initially helping me do the first bleed before i took it to my friends garage. I think she might have gotten really on the brake pedal and put it right to the floor a few times. I have heard that itself can damage some seals since its a bit of an over travel situation. But i don't have anything to back that up.
-
No i didn't....i used some pads that where about $40 from autozone. Not the cheapest, not the most expensive. Thats interesting though...strange.
-
I understand that. The reason i went front, then back, is because the front was the only section opened and only opened for a second. This started as a pad swap and turned into a brake job. Zero.. I did this job about 1 month ago...hoping it would get better and it hasn't. Looks like i'll have to get a real pro to look at it and bring back my pedal feel!
-
I did a front brake job on my Pathfinder. In order to get the pads back in, i had to bleed off a small mount of brake fluid. They just would not go back in. So, no problem, just re bleed. Well i rebled ALL of the brakes and even used a vacum bleeder, and still cannot get them to really hold good pressure. The truck does stop fine, but the pedal feel is not what it used to be. I also feel like i could not skid the tires even if i tried. The nipples are at the high spot on the caliper, so fluid will not drain out letting air in,,looks like a good design. My friend is a mechanic, so we had the truck on a lift and the process we used was this. -bleed the front (hand) -bleed the back (speed bleeder) -bleed the front again (speed bleeder) -crack the fittings at the master cyclinder under pressure...no air. -adjust the play in the back brakes,,they where fine. We went through about 1 quart of fluid, which was all the truck had in it. We where getting ZERO air bubbles. Is it possible a gasket was damaged in the master cylinder? I have never taken one apart, so i'm speaking from ignorance. No leaks found anywhere. Checked the whole system. Thanks for any help. Dave
-
I'm impatient! Ok,,i'll get together a "how-to" for an LED tailight conversion. I'll do it over Christmas vacation. Is this write-up going to cover both types of tail lights for the BB? I have a '99, its the two bulb 'stacked' formation. I replaced the lower bulb with a strobing led unit already. This will cover an LED conversion for the top bulb. However, with the method i'm using, you'll be able to do anything from a motorcycle led convesion to an auto.
-
I'm impatient! Ok,,i'll get together a "how-to" for an LED tailight conversion. I'll do it over Christmas vacation.
-
I like the old fashioned way. If the air pressure is low (or zero) the tires are dangerously greasey in the turns.
-
If you guys are interested, i'll post a "how-to" when i do my tail light retrofit with superflux leds. I should have it done in about 2-3 wks.
-
Yes, the plug and plays are limited by the size you can get through that buld hole in the back of the housing. Thats why i make my own. Only way to go.
-
Its really easy to make your own custom led bulbs. Buy some superflux leds, solder them to a board with some resistors, and you'll have an amazingly bright taillight for <$25. I retrofitting my front turn signals for about $8 each.
-
Brake fluid is designed to absorb water. That way you don't get pools of water in the system itself...it is in the fluid not pooling up. Condensation can be a big problem for brake systems.
-
DIY - Installing a RAM ball mount on a CBR1100XX
TuffguyF4i replied to Zero Knievel's topic in The Garage
I'm confused. Why not just use the ram stem mount? I used it on my XX w/o real issue. You just have to take the large cap off first. -
That looks so gettofab!!!
-
Stick a voltmeter across the terminals while on low beam. You got volts, you got low beam.
-
You should have a C spanner in your factory honda toolkit. Its the only tool in there that you'll never find any other use for!
-
I'm glad i have my $80 SS front brake lines, every time i hit the brake. Best mod, hands down. Second, would be getting tires that match the bike. I'm very happy with my Pilot Roads...nice profile.
-
Single side exhaust by capping one side of the exhaust pipe.
TuffguyF4i replied to LogoMan's topic in The Garage
Thats what i was going to say. You might get some weird stuff going on, noise and harmonics wise. Pipes really are tuned for the bike. If its what you want, i would try it...you don't have much to loose. -
I have a lightbar mounted below the plate on each of my bikes. On the XX i removed the lower bulb and replaced it with one of these. (red one) http://www.strobe.com/component/option,com...ufacturer_id,0/ Super bright strobe.
-
My general rule of thumb is 40miles after the light comes on. Works every time.
-
Not mine. http://hartford.craigslist.org/mcy/869975790.html