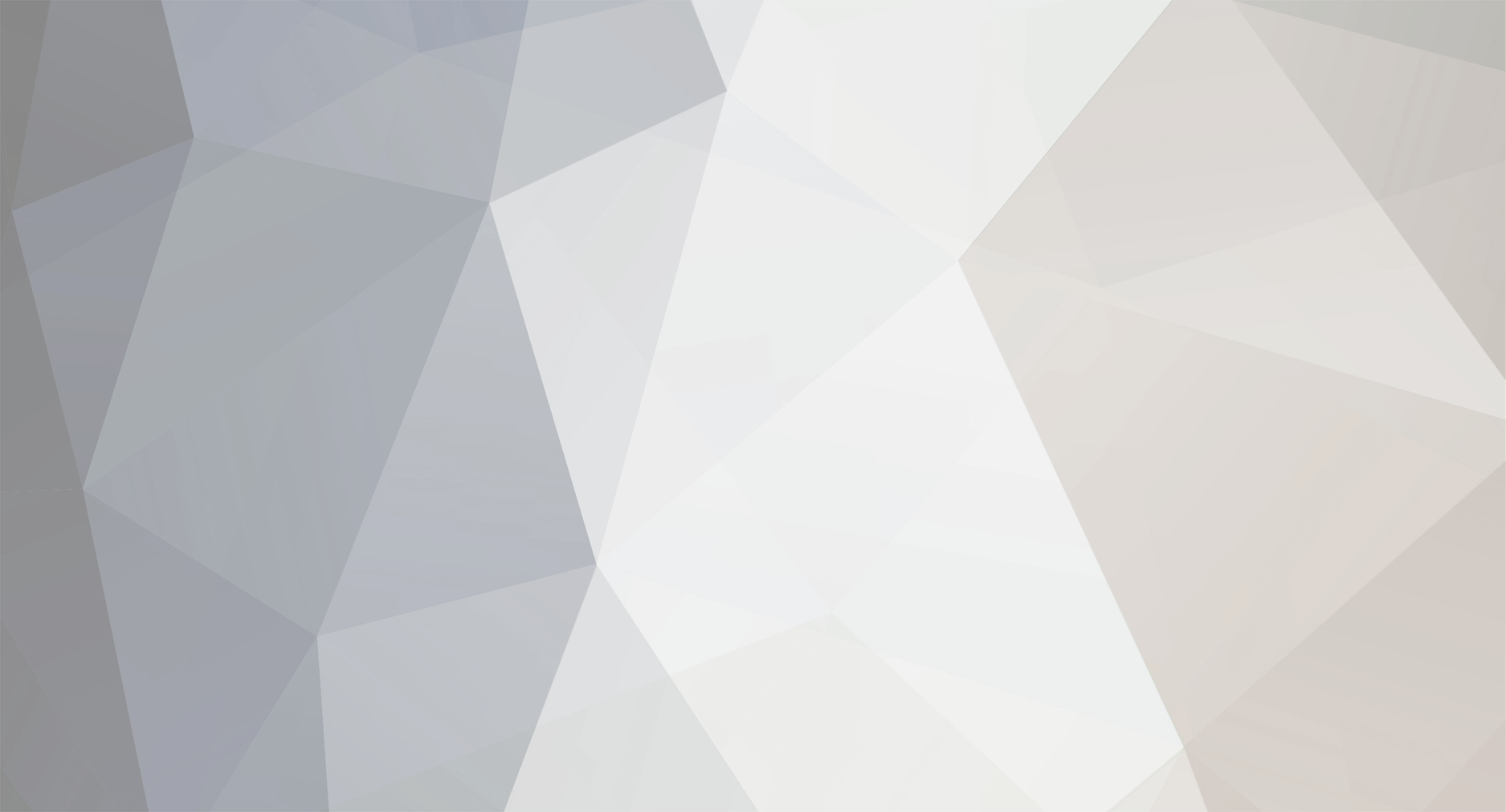
mickcbr1100
Members-
Posts
150 -
Joined
-
Last visited
Content Type
Profiles
Forums
Gallery
Events
Everything posted by mickcbr1100
-
Chris have you mailed Pete with the 1200 'bird at Blackbird Spares in the UK?, sure he could point you in the right direction as he has access to different exhaust systems and plumped for the Akra race giving 176 hp. There's a dyno printout on the page as well. http://www.blackbirdspares.co.uk/demobike.html
-
Nearly forgot - Pete from Blackbird spares has a 1200 'bird- puts out 176hp without the the ram air effect. Check out the spec http://www.blackbirdspares.co.uk/demobike.html Nice guy, no-one has a bad word to say about him I'm sure he'll answer any questions you may have Chris.
-
Chris if you didn't know V&M are no more, Jack Valentine decided to quit the retail side, just runs his racing teams now under the new name Valmoto http://www.valmoto.com/ if you need to contact them for any info. Also check out TTS who do a lot of big bore kits and all the other bits- valves etc and have specs on their website http://www.tts-performance.com/bigborepage...46a701cc2c06103
-
Like they said but some of the older bikes also had a PRI(me) position on the tap which would let the fuel out under gravity. To confirm its a vacuum operated tap it will have two pipes coming from it, the larger for fuel the narrower for the vacuum.
-
You got a bargain Chris, might have a busa killer come Spring. :cool:
-
You're my hero dude :cool: , a self confessed "if it ain't broke don't fix it" antichrist :twisted:
-
Nice :cool: no wonder why you're running out of space, a tool a week soon fills the house up :roll:
-
For the lathe you can buy a basic set of tools that will do most jobs probably $20-30 High Speed Steel or Carbide tipped would be good enough for alloy, mild steel, brass etc there are more specialised tools for boring large holes, cutting threads or harder metal eg stainless steel which you could get as and when you worked your way up to using them. The mill tools are the same spec as the lathe tools, face or edge cutters for the basic stuff then more specialised ones- different diameters and different angles- dovetailing etc. They can be mounted either in the chuck or via a taper or collet system depending on what you have. If you're buying new a lot of the machines include a basic set of tools for the machine that should get you going. It would be well worth your while getting a book on turning/milling as it will explain much better the different types of tools and cutters and what they are best suited for. What might look an ideal tool to say turn down a piece of aluminium may well do the job but leave the work a lot rougher than if you had used one with the correct cutting angle which would give you a lot better finish. Sounds complicated but once you've seen the type of tool that suits each job it becomes a lot clearer. C'mon Joe POST don't be shy :blowjob: Hey Eric you posting your pics of the Turbo Lawnmower and NOS Hoover ?
-
As Joe says not everyone has the space or money for the big industrial stuff, nice though it is you don't have to go big if its one off personal stuff you are doing. Don't have to go to ridiculously high rpm either to compensate for lower power you adjust it by taking smaller cuts, may take a bit longer but you're not an assembly line and still get there. We're not talking commercial here just DIY and people who think they might want to have a go starting from scratch.
-
I suppose the two most useful tools are the milling machine and the centre lathe. With a lathe the work rotates and the tool is brought to bear on it with a milling machine the tool rotates and the work brought to bear on it. As stated the mill is basically a precision bench drill so can be used just as a drill if need be but with the precision cross vise base table and the various cutters it can shape metal. Its best looked on as the metal equivalent of a wood router. You can get all types and shapes of cutter same as a router you're not limited to mounting the workpiece in a vise on the table you can use T bolts in the table slots to secure near enough anything you want. Everyone's seen a centre lathe it usually comes with a self centering 3 jaw chuck but you really need an independent 4 jaw chuck and a face plate as well to use its full potential so you are then not just limited to using round or hex bar. You can just work by trial and error from scratch with either machine but you're bound to make a lot of mistakes. Different metals need different cutting speeds different tool angles etc. I hadn't used a lathe for 30 years since school and college when I bought mine last year but soon got back into the swing making bits for the bike, just cosmetic, nothing load bearing, wouldn't like to replace anything that is critical with my limited knowledge. One piece of aluminium alloy looks the same as another but the specs can be totally different so you've got to know exactly what you're using and doing. There are quite few books out there on metal turning and milling and reading one will give you enough knowledge to make a start, you pick up more as you go along as to what works and what doesn't as long as you've got the basics to start with. Lathes are classified by their centre height - (distance from the machine bed to centre of the chuck which x2 gives you the maximum diameter you can work with) and useable length of bed which gives you the max length of your workpiece. Mines only 4.5"(9" workable) x 12" a budget model but its been OK for everything I've wanted to do up to now and you're not limited to just metal, if you want to you can use it for plastic, wood etc which I've done on many occassions making patterns and suchlike to save wasting metal. If you did want to get into metalwork you might consider the growing number of combined lathe/millers, the two combined into one machine is very versatile . The possibilities are endless as to what you can actually make or do with them the only limiting factor is your imagination, if you so desired you could even make copies of the machines themselves, self perpetuating so to speak. I've just been making bike bits but I've got a few other ideas on the go as well such as a fairly large scale bike model and suchlike and done the odd mod for things in the house. Sorry but I've got no idea as to US prices or what's available there. edit- sorry missed this link - saw the big muthas but not this one of Joe's %5burl=http://www.harborfreight.com/cpi/ctaf/Displayitem.taf?itemnumber=39743%5dhttp://www.harborfreight.com/cpi/ctaf/Disp...temnumber=39743" target="_blank"> http://www.harborfreight.com/cpi/ctaf/Disp...temnumber=39743 ://http://www.harborfreight.com/cpi/ct...=39743 It's a small machine but reasonably priced maybe an ideal starting point for experimenting to see if you can/want to get into it before moving up to something bigger and more expensive.
-
Its badged as a Chester but no doubt made in China like most are nowadays, costs £585 and the way things cost more over here probably be the same in dollars over there http://chesteruk.net/modelengineering.htm I'm sure if you bought one for the rearsets you'd soon find other uses for it afterwards there's always something you can find to improve on or customise to your own tastes, shall be having a go at rearsets myself eventually. Also they're only really a precision benchdrill with a moving vice table so there are a lot of other opportunities to use it as a drill.
-
Poll on Carrozzeria Wheels, Should Webmster seek a Discount
mickcbr1100 replied to ralfybebedosekys's topic in The Garage
Someone, in particular YOU as you are so impressed with them, are going to have to buy a set of these wheels to actually try them you cant expect anyone to buy them "blind". People on here mainly go by first hand recommendations from other members, cheapo accessories yeah great no problem but not something at this price someones got to try them first. It also works here that whoever fancies a particular item organises group buys not the site admin. -
Carlos mustn't have bothered to do the login settings for this section, probably hoping for some DIY genius, Norm or whoever to drop in :cool: I'm having this milling machine, will do me for what I want
-
New Carrozzeria Wheels, mass produced forged bargains???
mickcbr1100 replied to ralfybebedosekys's topic in The Garage
Why all the calculations? the wheels are only reducing unsprung weight which does improve handling but the only effect on performance is the actual reduction in the overall weight of the bike ie "7lbs = 1hp" or am I totally wrong again :oops: -
Depends what you're thinking of doing Carlos, my main interest is the bike, made frame plugs, bar ends, frame sliders up to now and got a few other things lined up some for the real world and also want to make a scale model from scratch but still undecided which bike it will be. I reckon lathe is #1 followed by a milling machine though I've used a cross vice on my bench drill as a miller on odd occassions, you can get the combined lathe and millers which are OK. The other power tools are cheap- bench grinder that also doubles up as polisher, bench drill and some kind of power saw for non ferrous metal. It's a bitch trying to cut 2" aluminium bar with a hacksaw, so soft it clogs the teeth up straight away my bandsaw goes straight through it no problem. All you really need then are some decent measuring and marking tools. Micrometer is more accurate but vernier gauge is more versatile and more than accurate for what I'm doing. Any other bits and bobs follow as you decide you need them usually because you think they look lonely in that tool shop or on that show stall and need a good home. :roll:
-
Just had a new shed a week ago, 10x6, not big but its all I could fit into the space the wife allowed me :roll: Just doing it out so I can escape to do my metalwork projects, got a small milling machine on order and a larger lathe is on the cards.
-
Try cleaning the clutch pushrod up first, get to it from behind the clutch slave cylinder, it gets all the crap off the front sprocket there, taking the rod out cleaning it and that area up does help. Clutch itself should be OK you'd be getting slip if it was on its way out. Doesn't seem to be an in between, its either quiet or rattles like a bag of spanners but has no ill effects.
-
You can take it off with a pin socket or whatever you make up but you really need the special tool to replace it to make sure its torqued up correctly, you could make one I suppose but you'd need the offset measurements off the proper tool to make sure you're at the right poundage as you apply the torque wrench off centre. The recent post in the garage from Mack? who had problems doing it up and kept losing chain tension until he used the proper tool backs it up. edit- found it http://www.cbr1100xx.org/forum/viewtopic.php?t=5419
-
Yup, same torque all years edit- Doh..great minds think alike at exactly the same time :roll:
-
The swingarm locknut could well be your problem, not done up right and allowing a bit of flex throwing the back wheel out each time you ride it. You really need the special tool to torque it back up correctly they're £60 over here so probably be $60 there, you think you get ripped off for Honda spares but you ought to live here!!. Be worth it if you're doing it regularly but if not take it to a Honda dealer for them to do it for you.
-
What Joe said plus there is a fairly common titanium/gunmetal? type colour in UK/Europe. Mine's a 2000 with this colour frame and wheels. It's going to be a bitch to colour match you'd be better off going for a contrasting colour or polishing them.
-
Think the concensus of opinion is to use the EBCs as they come without the Honda shim. That's how I and others I know do it with no problems.
-
Fair point about removing the actual wheel but anything else including the chain tensioning can be done with the spools in the spindle/axle. I've only bothered to use it once when I was removing then replacing the centrestand as it was a lot easier than just using the sidestand. The swingarm is box section alloy you couldn't drill and tap it for spools and be sure they would hold unless someone has ever taken an angle grinder to one and cut it up to find if there is a suitable point to tap a thread. A hole straight through the arm bolting the spool right up might work but again without knowing the thickness of the alloy at that point I wouldn't like to try it.
-
Gotcha :cool: I can live without it, I ride to get away from it all not to have something squawking in my ear all the time, my limit is a phone which is kept in my pocket.
-
Wrong?? in what way?? , It is a genuine product if thats what you mean. Vemar has been going years, its an Italian company, and do a web search on Vemar VSX quite a few entries.