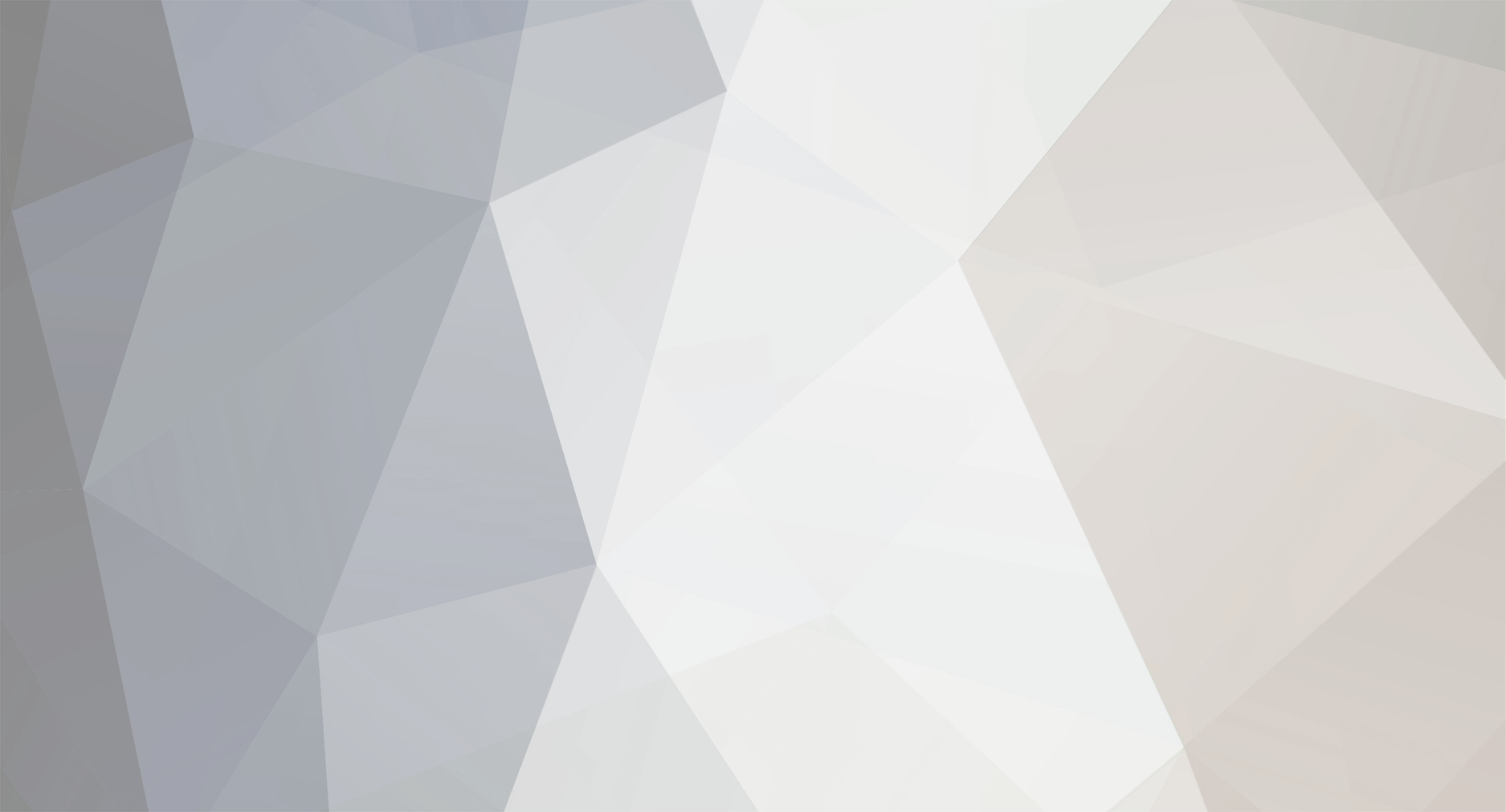
Warchild
Members-
Posts
1,377 -
Joined
-
Last visited
Content Type
Profiles
Forums
Gallery
Events
Everything posted by Warchild
-
If you want to PayPal me some $$$ to cover postage/insurance, sure man, I'll lend it to you. PM me your address when you're about to do your bearings....
-
Alright, then....... Installing the tapered steering stem bearings proved to be a piece of cake. You need three items to do this: 1) a 10” steel or brass drift 2) a 5lb mallet or heavy-duty hammer 3) a foot-long section of 1 ¼” I.D. steel pipe. Below is the part number of the AllBallsRacing.com tapered beariong kit that I installed: Using a nice Harbor Freight 10" hardened steel drift and 5lb mallet, I popped the old races out easy as could be. As you look down the steering neck opening, you will see there are two large opposing notches near the bearing races. These notches provide an ample perch oportunity for your drift. You'll be able to place a large section of the drift directly on the bearing race you’re driving out. The two races popped out with no issues. Below are the OEM ball bearings after they are removed. The set on the right is the lower bearing; the race on top is what you'll use to drive the new tapered bearings (lower) into place. And the others you'll use to drive the new tapered bearing races into their respective recesses: Here's the upper stem tapered bearings on a test fit prior to the grease packing job: And here's the first of many grease-packing strokes (<insert gay-ass joke here>... ) Below, I am using the trusty Mobil One Fully Synthetic Universal Grease to pack these tapered babies: On the right you see the three main hand tools needed: 10" drift, 5-lb mallet. 1 1/4" I.D pipe approx 12" long. Using the OEM lower race as a drift, here I have just finished driving the new lower tapered bearings onto the bottom of the steering stem. At this point, the steering stem is wiped free of excess grease, and re-inserted into the frame neck. I am happy to find the Blackbird takes the exact same steering torque tool as my old ST1100, so I am blessed with already having the correct tool for the job. The upper brace is torqued the 25 Nm, then worked from stop-to-stop several times, then retorqued to the same setting again. A lock-tab washer is inserted before the final locknut is snugged up and locking tabs aligned. Here is that spendy-ass Honda Steering Stem Socket p/n: 07916-3710101 seen here sitting atop the steering stem just before I moved it to install the upper triple-tree: All done!
-
Well, I have two Wilbers, one in the Blackbird and the FJR, and about a combined 27,000 miles between the two since installation. Both work perfectly (huge improvement on the FJR in particular), nary even a hint of any seepage anywhere.....
-
I assume you meant 17 volts, and yeah, that ain't necessarily a good thing The fact that you can't reproduce it is encouraging, however. Could've been just a meter glitch, I suppose.
-
If this reading is taken at an engine speed no lower than 3000 RPM, and you have no other electrical accessories running, bike's all stock, only the low-beam burning, etc, then IMO, this output is just a pinch on the low side. Adequate perhaps. But not really where it oughta be. With a truly healthy charging system, including a relatively fresh battery, you should see your voltmeter pushing somewhere in the 14.2v - 14.5v range (thereabouts) in the conditions described above. How old is the battery (both in years, and in mileage)? How many miles on the bike? Are the stator and R/R original?
-
Re-post of my CCT install that was lost when we switched servers..... HTH......
-
All you goodamn maggots can just suck moist ass!! You suck because I know you're right, I'm just being lazy. *sigh* Well, shit.... I'll give CBRBearing.com a call in the morning, then.... Fuckers. No. Got a linky to it?
-
That is the question..... And I think the answer is "no" for me right now, because even though I realize tapered steering head bearings are the way to fly.... the fact of the matter is: my OEM hardware still looks in good shape, and I've never had any issues with front end tracking/steering, so... why do I want to go through the expense and hassle of pulling out perfectly good races? So I think I'll just re-pack these bearings, and move on to the next item on the long list of TLC I'm bestowing on Night Train here...
-
The proper way is to bite the bullet and remove the forks. Doing so is considerd an ass-pain to some, but it's the way to go if you care about doing the shit right, getting a thorough, proper drain. You can, if you want to, opt for leaving them in place and draining them via a cartrige retaining bolt at the very bottom of the fork leg. It's an option, though I personally don't recommend it. After you remove the fork off the bike, thoroughly clean that slider tube since you'll be pumping the fork leg quite a bit during this exercise, and you don't want any crusty bugs or other debris to dork up your fork seals as you work the forks: Hopefully you remembered to loosen the 24mm top cap prior to removing the fork from the bike: After the fork is removed and the 24mm top cap loosened, you can pull down the spacer tube to expose the 14mm locking nut. You (obviously) need to hold the top cap with the socket while you take a 14mm wrench to loosen the locking nut: Now that the top cap is removed, you can remove the long spacer tube: And pour out that nasty-ass old fork fluid (pour it in a measuring device if you want to know the exact amount of fluid you removed): After the tube is close to being upside-down, get ready to catch the spacer ring and fork spring and they emerge from the slider tube. Pump the tube (and the damper rod) many, many times to try to get every last drop out that's going to come out. Some guys hang their forks upside down overnight (over a container, obviously) to get a uber-thorough fork oil drain: As you can see, I only got about 15oz of fork oil out this fork: Basically, the procedure for obtaining the 150mm air gap height is to dump around ~375mm of fluid in the collapsed fork leg, reach in and pull the damper rod, and pump the damper rod up and down, *slowly*, a good 15-20 times so that the new fluid is thoroughly dispersed throughout the fork's inner workings. Now, again, with the fork springs NOT in the tube, and the fork leg *fully* collapsed, add suspension fluid until the level is exactly 150mm from the top edge of the fork leg. Once this is done, you reach in for the last time and pull out the damper rod to it's max extension, quickly slip the fork spring over it and "catch" the damper rod before it slowly settles back down into the tube (as you can no longer reach it if it settles to the bottom since the springs are now in the way). Now slip in the spring seat washer, and finally the long spacer tube. Thread on the top cap and lock it down with that 14mm lock nut seen above. Now just raise (extend) the slider tube up high enough so that you can thread that top cap down into the slider tube. Torque down the top cap to spec, re-install the forks, and you're done...
-
-
Absolutely correct. Specifically, the outboard pad, which is the lower of these two pads: As you can see below, I caught this one just prior to having it start scoring up the rotor: The movement/action of the secondary master cylinder above the left caliper is the cause of this unusual "sloping" wear pattern. These are my original front left brake pads at 27,000 miles.....
-
And not just "within tolerance"....... 15 of the 16 were still smack dab in the center of the spec range! The inboard exhaust of #3 cylinder was just a tiny bit tighter than the others, but still well, well within the range, so I'm not yanking the cams to mess with it, Concur that this motor is one understressed, overbuilt bastard....
-
It is, IMO, somewhat of an ass-pain to work around the frame to check the valve clearances... but slightly less painful than to pull the motor altogether.
-
Well, now that I (thankfully) don't have to pull cams and adjust the shims, I'm ready to send the shim bank off to whoever needs it next.....
-
For my well-behaved valvetrain, I attribute about 95% of it simply to righteous, clean living, and about 5% of it due a lifetime of Mobil One at 4500-mile change intervals.
-
Well..... I felt guilty about it. That, and the fact the 'ol Night Train is going to see some exceptionally heavy-duty Endurance rally work this summer. Five separate events in the hot Desert West between May and August. I'll be spending considerable time blazing at supra-legel speeds for 24-36 hours straight. So the bike is getting some serious TLC this winter, and also some brand new killer mods that need extensive testing before they are used in competition.
-
Fucking-A, dudes!!! I'm a happy mo-fo tonight! Just got through performing a long, long, LOOOOOOOOOONG overdue valve clearance check.... like it's been over 55,000 miles since I last looked at 'em..... Thankfully, 15 of the 16 valves were absolutely DEAD NUTS in the middle of spec! The inboard exhaust valve on cylinder #3 is a pinch tighter that the others, it measured out at .210 mm. All other exhaust valves measured out at .223, and every single intake measure out at .155 mm. No pulling the cams this time... WOO-HOO!!!!!!!! Over 73,000 high-speed miles under some very arduous Endurance Rally conditions, and *still* haven't had to adjust a valve yet!
-
Concur with Rockme.... I'm pretty sure Klaus would want to know about this.... I'll point him to this thread when he gets back from vacation....
-
You could try taping up the threads and powder-coating the heads black.... :idea:
-
Installing the Wilbers Fork springs
-
Yep, I believe so... Check the Pazzo site for available models
-
Well, I just launched the Pazzo Group Buy in the Pub (since so few seem to go anywhere near the Garage!), So go snap them up, dudes! :twisted:
-
No, the adjuster is always on top, where you can actually get to it and adjust it while underway.
-
Yep, I just saw an email from him to that effect..... he overnighted them, they oughta be here Monday... Assuming no fitment issues, etc, the Pazzo Lever Group Buy starts early next week!!!!!!!!!! :thumbsup:
-
C'mon Dale do your thing. :wink: [-o< I have been ready, but Mike wanted me to wait until I receive the Pazzo Levers and test install them before starting the GB..... And they were supposed to have been shipped already! If you saw them still there today, Randy, I'm fixing to be bummed out.... :evil: